OSHA needs proof that companies are doing the right things for employees in terms of health and safety. But how is your company supposed to determine what is right? Being OSHA compliant can be a challenge. Companies not only have to provide policies, training and checklists that comply with OSHA requirements, but also bear the burden of determining what it means to be compliant. While OSHA provides extensive guidelines, following them is not always straightforward.
Every company has its own facilities, equipment, workforces, and procedures. Large companies might also operate across jurisdictions, with different kinds of warehouses and workspaces, in different weather conditions, with a wide range of materials and employees of varied experience levels. Every single detail that goes into a company’s operation has he potential to interact with an OSHA requirement in some way, making OSHA compliance a puzzle with many moving parts. How can companies ensure they’re OSHA-ready? How can companies determine what the right checklists, policies, and procedures are for the varied and unique situations they face? More importantly for your bottom line, how can you make sure you’re OSHA-ready in the most efficient, flexible and productive way? The key is smarter safety through digital inspections.
Preparing for OSHA with digital inspections: proof, rigor, and flexibility
OSHA guidelines are written broadly to apply to as many situations as possible. As a result, companies and employee scan encounter difficulties translating OSHA provisions to their own facilities, circumstances, and ways of doing things. OSHA provides generic checklist samples, but it is up to you to assess how they apply to your work environment. Exacerbating the problem is that OSHA’s “if this, consider that” scenarios can be too vague to ensure full compliance by inexperienced employees. Regardless of who undertakes the inspection, OSHA demands that proof be provided to the same rigorous standard.
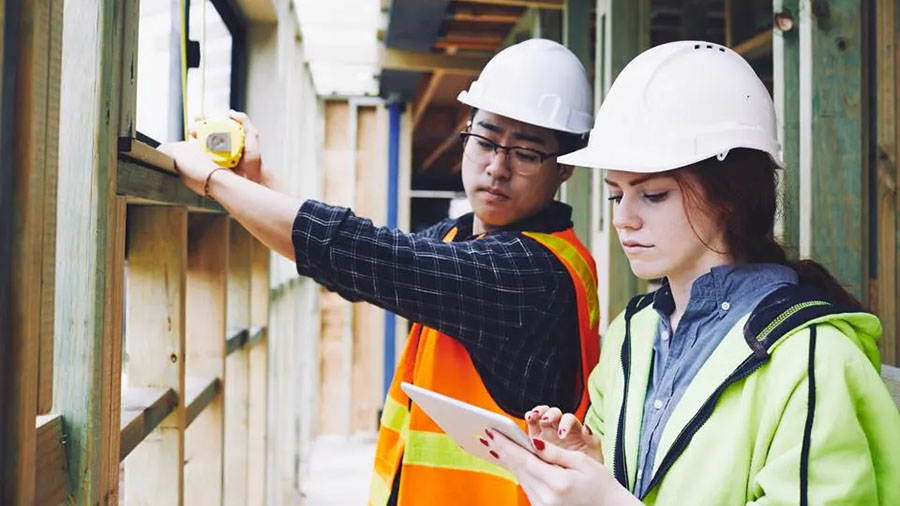
Consider a seasonal employee in a distribution company instructed to do safety checks on order pickers in the warehouse. On the OSHA website, order pickers are listed under “Powered Industrial Trucks.” While it’s a straightforward inspection, the employee can get bogged down in minutiae that doesn’t apply to the types of vehicles being inspected, wasting time, and potentially generating useless data. Ultimately, if companies don’t supply workers with the kinds of streamlined checklists needed to complete their work, the company risks running afoul of OSHA compliance.</p></p></p></p></p></p>
The best way to avoid this issue is to build custom checklists for compliance that ensure precision and consistency. One of the first questions OSHA incident investigators will ask is, “Did the employee receive adequate training to do their job?” The data and documentation a company gathers and submits to OSHA needs to answer this question clearly and unambiguously – and digital inspection checklists do so in an uncomplicated, powerful, and data-driven way.</p></p></p></p></p></p>
The problem with paper
Most companies use a combination of spreadsheets and paper-based media to keep safety, training, and compliance records. Once the record is recorded on paper, employees must then take the time to translate paper documents created in the field to Word documents and Excel spreadsheets, allowing the introduction of inaccuracies at every step. The entered media is unwieldy to use, error-prone, and time-consuming to create, edit and maintain. Adding to the inefficiency, paper- and spreadsheet-based reporting can be chaotic and messy when it comes to version control. One worksite might have local copies of checklists that they printout and use, never realizing on the company portal newer versions exist that may reflect OSHA amendments.</p></p></p></p></p></p>
There may also be differing conditions and requirements at each warehouse: for example, one warehouse may have a refrigerated section while others do not, and thus will have different safety requirements. Despite these differences, companies need to be prepared for scheduled and unscheduled OSHA visits to any location and be ready with equally comprehensive and up-to-date safety reporting at every worksite. Working exclusively with paper, Word files and spreadsheets leads to gaps in compliance, while version control issues can prevent you from providing just-in-time reports.</p></p></p></p></p></p>
Limitations of paper-based reporting
Scenarios are always changing, and companies need far more flexibility over compliance reporting than paper can provide. When a company acquires new equipment, for instance, along with it comes new checklists and additional training. It’s not easy to integrate this new data into a paper-based reporting system. Not only that, but OSHA guidelines themselves are frequently updated – just consider the new sanitization and PPE protocols that were introduced due to COVID-19. Manufacturing changes can also lead to updates and amendments in OSHA guidelines. Regardless of the source, these modifications will affect the checklists and measures you’ve already put in place.
Paper is difficult to standardize across sites and situations, doesn’t provide the kind of rigor OSHA demands, and can’t deliver just-in-time capabilities. It simply can’t provide the kind of control and the capability that’s available with digital inspections.
Better data with digital inspections
Digitization not only solves the problem with paper, it lets organizations work smarter and more efficiently as they streamline and optimize their OSHA compliance procedures. Digital tools help companies become agile end-to-end and prepare them for all kinds of reporting demands in ways that show a major return on investment.</p></p></p></p></p></p>
For starters, digitization solves versioning issues by furnishing everyone with the same information at the exact same time. Your company can create safety and inspection checklists tailored to specific equipment and information, such as small, powered trucks or lockout/tagout procedures, and provide them to all your mobile teams. When necessary, updates can be done in real-time and provided to all sites on the fly. Digitization and automation give companies the rigor they need to be responsive to OSHA, and the flexibility they need to account for changing scenarios, equipment, personnel, worksites, and the OSHA guidelines themselves.</p></p></p></p></p></p>
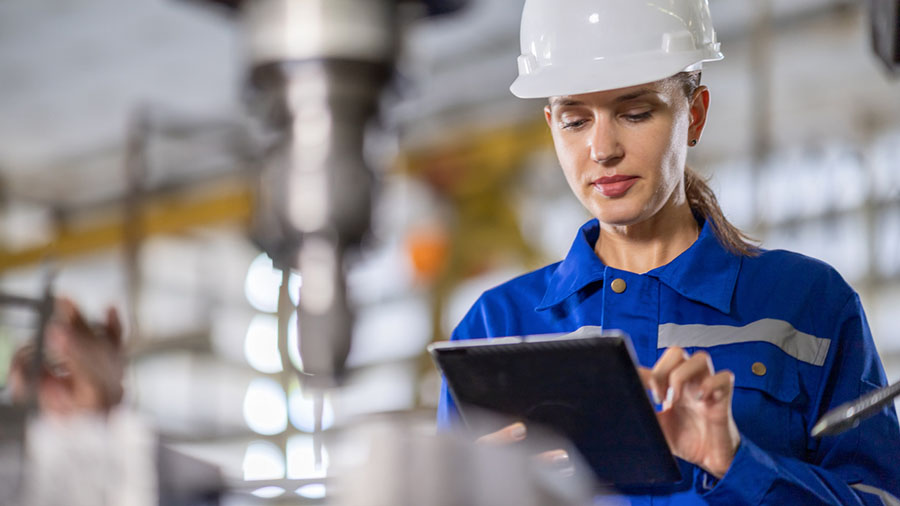
Additionally, digital inspection apps that provide tightly organized sets of descriptions and reference materials, including visuals, at the point of use can significantly reduce the likelihood of occupational injuries among inexperienced workers. For instance, if employees are using safety lanyards while working at heights, OSHA requires the second lanyard be connected before disconnecting the first, while apps can include reference photos showing DO and DON’T versions of this situation and others. In further use cases, visuals can be provided to help employees meet scaffolding specifications or to guide employees during equipment installations, such as choosing the right electrical outlet for kitchens and restrooms as opposed to water-free environments.</p></p></p></p></p></p>
Streamlined compliance
To make work easier, dropdown menus can expand to signal to employees checking for equipment or site safety that they need to supply more detail or hide extraneous checklist fields to make their work easier and still comply with OSHA requirements. Consider the OSHA sample checklist for Powered Industrial Trucks: although order pickers are among the vehicles in that list, some OSHA requirements for the broader category are inapplicable to that equipment. In contrast, here’s what a digital inspection checklist can do:
If it isn’t an order picker being inspected, the checklist hides those order picker questions. If it is an order picker, then OSHA-required fields specific to those vehicles are opened inside the app. This kind of simple, decision-tree checklist makes safety and health inspections simpler, more rigorous, and responsive to OSHA guidelines.
Tailoring digital checklists reduces worker errors, easing training for less experienced employees. It also aids in capturing valuable safety data efficiently. A safe worker is a productive worker, and a safe work environment is a productive one.
Make safety data highly accessible
Digitization enhances data completeness and accuracy for OSHA, while also automating data availability. Companies with the capability to generate rock-solid reports on-demand can meet OSHA’s reporting requirements. They can do this on a scheduled basis or in response to incidents, injuries, or complaints. This capability enables companies to respond to OSHA inspectors during unscheduled visits. They can share information about site safety, procedures, safety training, and personnel. Additionally, it allows for instant availability of records and incident reports to any visiting OSHA representative.
The ability to respond quickly is crucial in safety issues like equipment injuries or falls from scaffolding. Having all data related to a specific area of the map helps companies respond comprehensively. For example, a fall from scaffolding might require scaffolding inspections, toolbox talk records, and location data. Additionally, having access to personnel data, previous inspections, and incidents is essential. This comprehensive data allows companies to fully understand incidents, especially with OSHA information requests within 12 hours.
A safety investment that pays
Committing to OSHA guidelines is crucial for a company’s regular operations. Additionally, safety yields dividends across its entire organization. Companies that do safety well are already investing in tools and personnel to support their reporting and compliance measures. However, by digitizing work processes, companies realize the maximum ROI out of investments in safety. Having digital inspection data available for OSHA brings the following additional benefits:
Lower costs
Construction companies can use data to lower EMR and insurance rates.
Ensure profitability and operating stability
Rock solid compliance data is crucial for all industries, but for some, such as construction, even a day’s work stoppage can make a huge difference in profitability. Good data can help companies anticipate and prevent safety issues.
Turn safety into a key differentiator
Having a great program in place to track metrics proves that your company has an excellent safety record. Implementing a safety program shows you’re constantly working to make your safety record better. You can confidently tell partners that your buildings, warehouses, equipment, and staff are the safest. Then you can deliver the data that proves it.
Make safety smarter
Digital data can be leveraged to feed back into workflows and enterprise systems downstream to make smarter safety decisions.
Investing in digitization helps companies meet and exceed OSHA safety and reporting requirements on time and on-demand with better data, better analytics, and more useful reports. Isn’t it time you made the jump to digitization and got smart about safety?
Why wait?
Join the over 2,500 Fulcrum customers who have improved field inspection processes and streamlined reporting with real-time, scalable data sharing. Sign up for our free 30-day trial today!