Keeping up with ever-changing environmental regulations can be a challenge, but for environmental engineering firms, it’s paramount for serving their clients as well as preserving the environment. In fiscal year 2019, the Environmental Protection Agency required companies to invest more than $4.4 billion to control pollution (called injunctive relief) and pay more than $360 million in civil penalties. Continuous, centralized recordkeeping is critical to ensuring compliance and avoiding penalties like these. That’s why today’s environmental engineering firms are adopting mobile environmental compliance technology to make sure they’re helping their clients meet state and federal regulations. It also helps them work more efficiently so they can complete more jobs in less time without sacrificing quality.
For example, take the case of global environmental engineering firm Brown and Caldwell, which specializes in water and wastewater engineering. Adopting mobile technology in the field has enabled them to deliver results faster — and at a lower cost — to its customers.
Here’s their story.
Tackling a pressing public health issue with paper
Brown and Caldwell was hired by DeKalb County, GA to inspect 60,000 manholes as part of a project to reduce sewer overflows in metro Atlanta. Sewer overflows can cause serious water quality problems and back-up into homes, which not only causes property damage, but can threaten public health.
For the first half of the project, the engineers collected historical data and put it into their geographic information system (GIS), then exported it into paper map books that crews would use to try to locate the manholes.
When inspecting the manholes, the engineers used paper forms to collect data on their condition, and took tens of thousands of photos with digital cameras that would later have to be matched up with the inspection records. Then, another team of surveyors equipped with GPS would follow to affirm the precise location and elevation of each of the structures.
This was a huge, complicated undertaking, especially when it came to manholes in areas that had been redeveloped. And the longer the project took, the more Atlanta residents were at risk of being exposed to raw sewage.
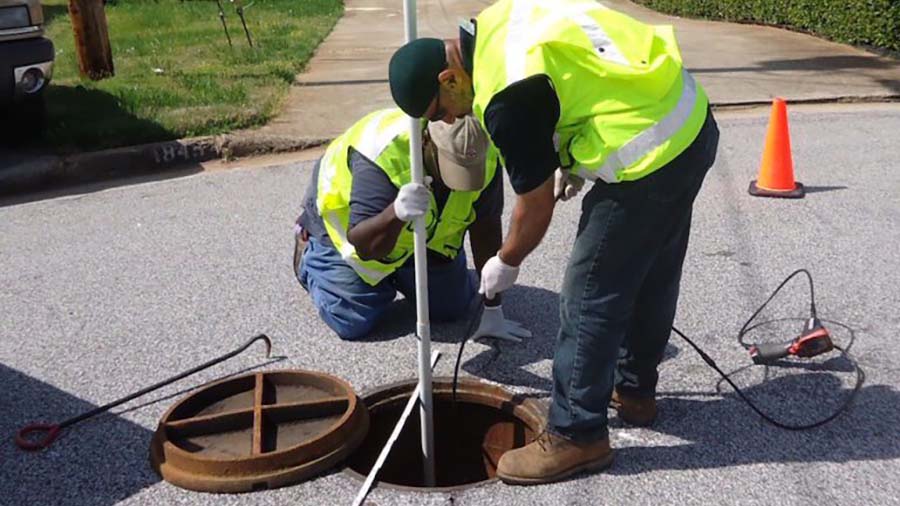
Getting better, faster data with no-code mobile apps
In the project’s second stage, Brown and Caldwell adopted Fulcrum’s no-code platform. This platform enhances mobile data collection and workflow automation. Equipping engineers with Fulcrum on their devices, they integrated paper map data with their GIS. Additionally, the system automatically linked field photos with the relevant assets.
As a result, fieldwork became more efficient. The team saved significant time by automating photo-inspection record matching. Moreover, inspection crews could reposition manholes. This adjustment made them more visible to following survey crews.
All data converged into a unified database. Thus, authorized users could access it instantly. They used smartphones, tablets, or the Fulcrum web dashboard for access.
Despite working on mobile devices, the crews faced no connectivity issues. Fulcrum’s offline capabilities ensured data collection continued uninterrupted. Once connectivity was restored, the data synced automatically.
After the project, Brown and Caldwell noted a 30% reduction in data management and QA time. Consequently, they addressed sewer overflows more swiftly.
Want to learn how you can leverage environmental compliance technology to streamline your field inspections to improve compliance, quality, and safety? Download the e-book, Top Opportunities to Modernize Your Field-based Inspection Processes!